Centrifugal Galvanizing

Table of Contents
Advanced Centrifugal Galvanizing Solutions by ANI Metal
In modern industrial galvanizing plants, achieving a consistent, high-quality zinc coating on small to medium-sized components requires more than just immersion in a hot zinc bath. The ANI Metal Centrifugal Galvanizing System combines precise thermal control with high-speed rotation to remove excess zinc and deliver uniform, drip-free finishes—boosting throughput, reducing waste, and elevating overall plant efficiency.
How Centrifugal Galvanizing Works
Immersion Phase
Parts are lowered into the hot-dip galvanizing kettle to ensure complete zinc penetration and metallurgical bonding.
Rotation Phase
Immediately after immersion, the system’s turbine-driven basket spins at adjustable speeds (up to 1,200 RPM), flinging off surplus zinc.
Drip Tank Recovery
Separated zinc droplets fall into a dedicated drip tank, where they solidify and are recycled back into the main bath—minimizing material loss.
Cool-Down & Discharge
Components exit the centrifuge fully coated, with a smooth, encapsulating layer free of runs, drips, or irregular thickness.
Key Features of the ANI Metal Centrifugal Galvanizing System
Variable Speed Control: Fine-tune rotation rate to match part geometry and desired coating thickness, ensuring optimal metal protection solutions.
Heavy-Duty Basket Design: Corrosion-resistant stainless steel baskets endure continuous exposure to molten zinc and repeated high-G forces.
Automated Sequence Programming: PLC-driven operation synchronizes immersion time, spin speed, and drip-tank cycles for consistent results and minimal operator intervention.
Integrated Safety Enclosures: Heat-insulated guards and emergency-stop interlocks protect personnel and comply with stringent plant safety regulations.
Modular Footprint: Scalable configurations allow easy integration into both new installations and retrofit projects across varied production capacities.
Operational & Environmental Benefits
Uniform Coating Quality: Eliminates “edge build-up” and uneven film thickness, delivering smooth, defect-free finishes that meet ISO galvanizing standards.
Zinc Savings: Recovers up to 20 % more zinc through efficient drip-tank collection, lowering raw-material costs and waste.
Increased Throughput: Rapid spin-dry cycles reduce total processing time by up to 30 %, boosting plant productivity and on-time delivery.
Reduced Labor: Semi-automated handling cuts manual finishing and cleanup tasks, freeing operators for value-added activities.
Lower Emissions: Controlled zinc recovery and enclosed drip collection help meet environmental permit limits for fume and particulate discharge.
Installation, Maintenance & ROI
The ANI Metal system installs seamlessly alongside existing galvanizing lines. Routine maintenance—such as periodic bearing lubrication and filter-bag inspections—takes less than 30 minutes per week. Most customers realize a full return on investment within 9–12 months thanks to lower zinc consumption, faster cycle times, and reduced rework costs.
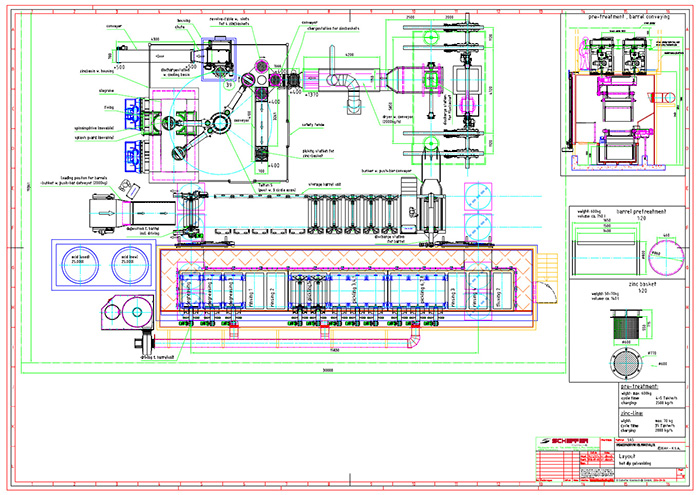
Centrifugal Galvanizing – Hot Dip Galvanizing | ANI METAL
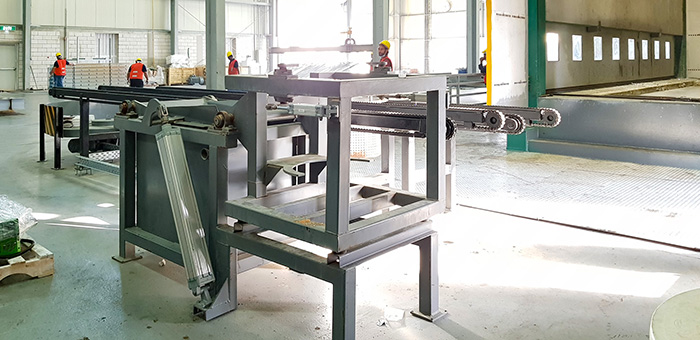
centrifugal galvanizing